The hemp fibre industry in Canada is in its early stages of development. As of 2015 there are no full–sized, commercial decortication facilities, but a few pilot scale plants operate on the Prairies including Vegreville, AB (operated by Alberta Innovates - Technology Futures, Figure xx) and Plain Industrial Hemp Processors at Gilbert Plains, MB. A number of fibre separation plants coupled with biocomposite manufacturing lines (hempcrete, bioplastic, fibre mats, insulation, etc.) will be constructed in southern Alberta in the foreseeable future. Some smaller facilities focused on processing hemp fibre for textile applications are also likely to appear on the Prairies.
Each commercial processing plant will be extending specific requirements regarding management of hemp harvest, including straight fibre cutting or post-combine straw, retting, etc. Straw specifications will depend on the end use of the fibre. Until the hemp fibre market is fully established, the processors will buy existing inventory of hemp stalks (primarily post-grain harvest material) but eventually will contract acres of hemp as a designated fibre crop and will develop their own harvesting protocols.
The decortication plant at Vegreville has been in operation since 2010.
This research and pre-commercial production facility operates the Van Dommele processing system with a straw input of 1 tonne per hour.
The system is particularly suitable for generating bast and hurd fibre for various biocomposite applications; however, it has limited capability to refine fibre for textiles. The facility offers flexible configurations of the cleaning and refining steps and therefore is particularly convenient for companies developing and testing new applications for various types of hemp fibres.
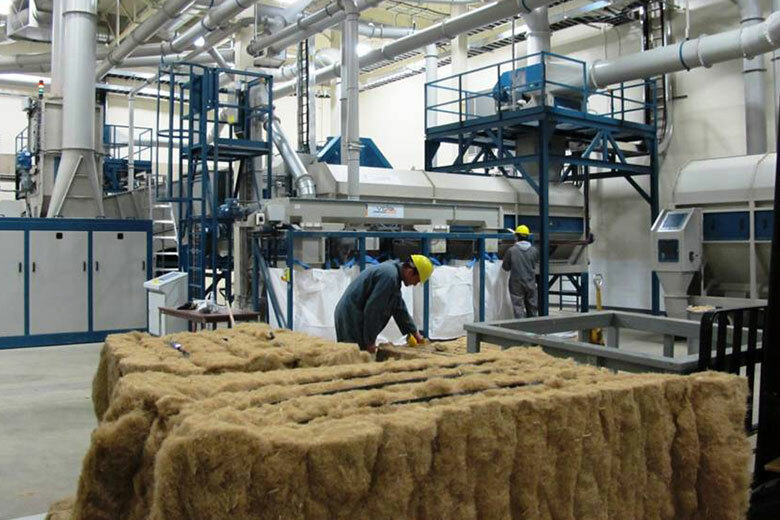
Figure xx – Hemp fibre decortication facility at Vegreville, AB
Plains Hemp is a fibre processing plant under construction in Gilbert Plains, MB. Plains Hemp is specific in the fibre that they will contract.
The contract specifies to supply only the fibre that is left between the combine rows (Figure xxi). They do not want the lumps and tangled fibre that is left behind the combine. For example a farmer combining the hemp with a 35 foot straight header would swath 20 feet between the rows of standing stubble.
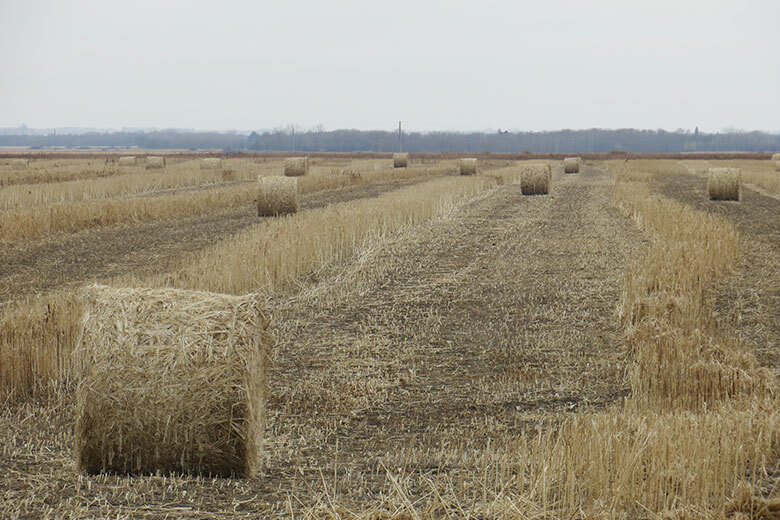
Figure xxi - Hemp swathed between combine straw rows
Dun Agro hemp harvester:https://www.youtube.com/watch?v=10DU5biagMA
John Deere hemp/flax harvester:https://www.youtube.com/watch?feature=player_embedded&v=vb6MvPBPnL4
Decortication of hemp straw results in two major types of fibre, hurd and bast(Figure i and ii). While both types of fibre can potentially be used in a plethora of industrial applications, few hemp fibre based products appear to have the potential to be successfully commercialized on the Canadian market in the foreseeable future. Here are the most promising applications:
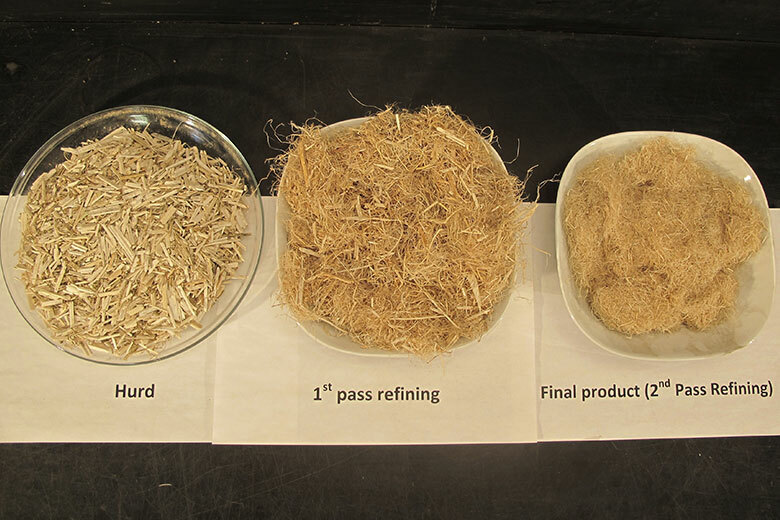
Figure i – Decorticated hemp straw generates hurd and bast fibre
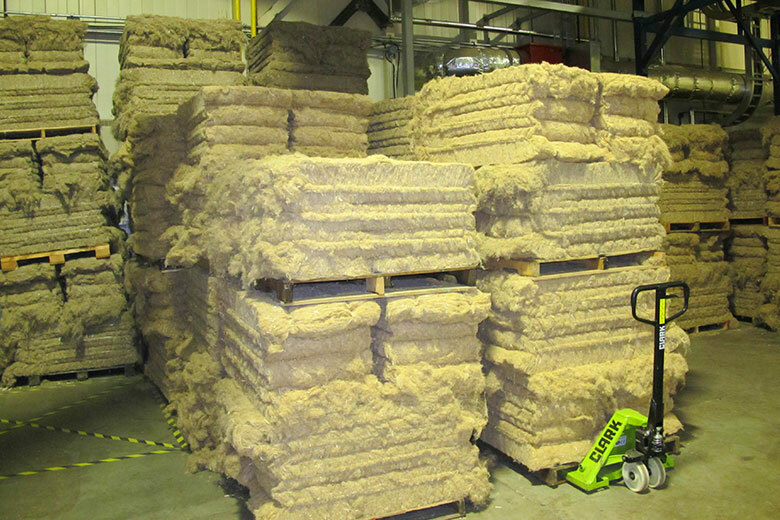
Figure ii – Refined bast fibre bales
Hurd Fibre
- Hempcrete – A biocomposite material consisting of hurd, lime, water and a binder. This product is expected to be a primary driver of the Canadian hemp fibre industry as large volumes of hurd feedstock are required by the emerging bio-building sector. (Figure iii and iv)
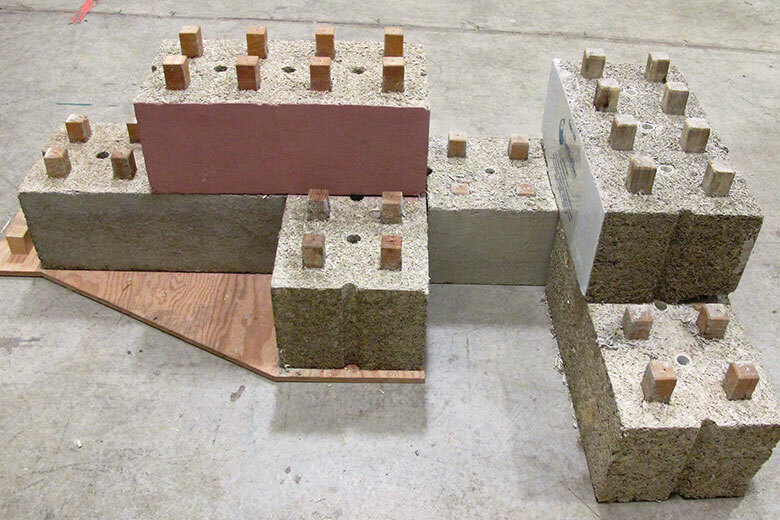
Figure iii – Hurd based building blocks
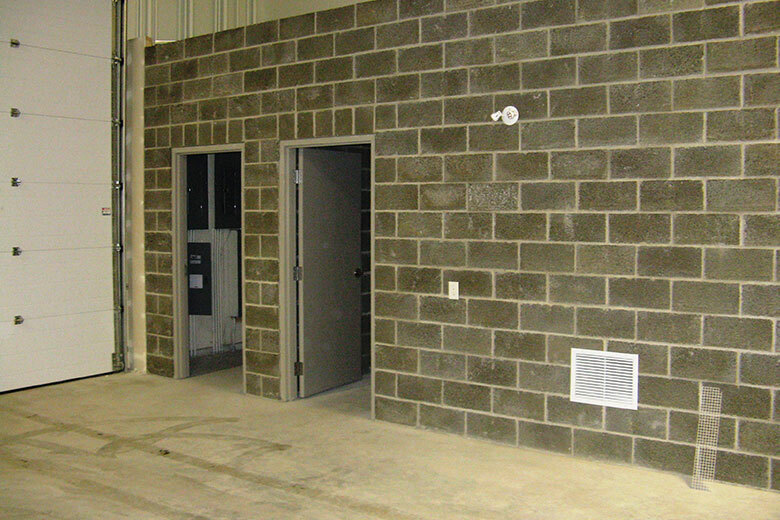
Figure iv – Wall constructed of hemp blocks
- Bedding materials - Owed to its superior absorbency properties and low dust content, hurd is widely recognized as a high performance bedding for farm animals (particularly horses) and pets.
- Absorbents – Hurd has application in the oil and gas industry as a high capacity material used for cleaning up spilled drilling muds and other harmful effluents.
- Particle boards – Hurd may serve as a high grade wood replacement in some applications, i.e. furniture making (Figure v).
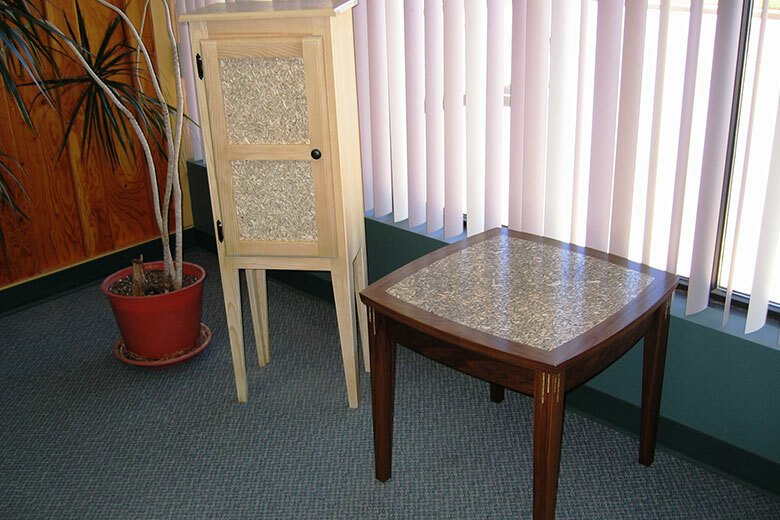
Figure v – Furniture made of hemp particle boards
- Ceiling panels and decorative plasters – When made of hurd, these offer great sound absorption and aesthetics.
Bast Fibre
- Plastics biocomposites – These can be made using compression and injection moulding processes. For example, bast fibre mats infused with resins replace fibreglass in composites used by the automotive industry, making hemp parts lighter and easily recyclable (Figure vi, vii). Similar advantages are offered from bast fibre in injection moulded products (Figure viii).
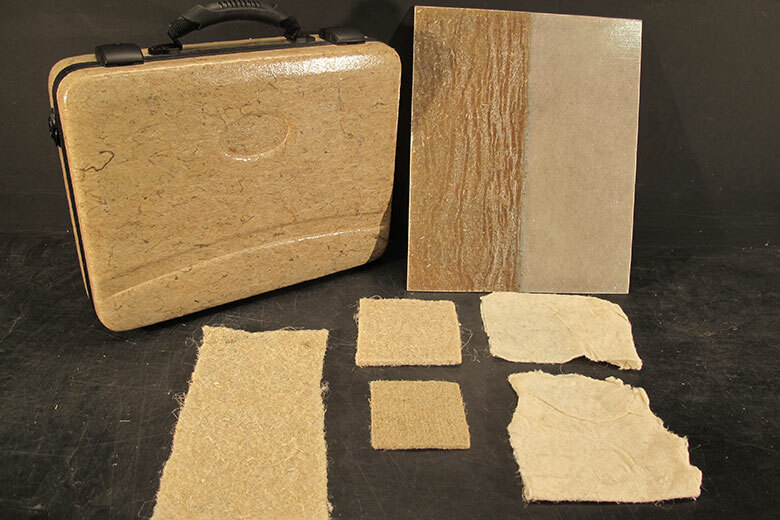
Figure vi – Fibre mats and their bicomposite applications
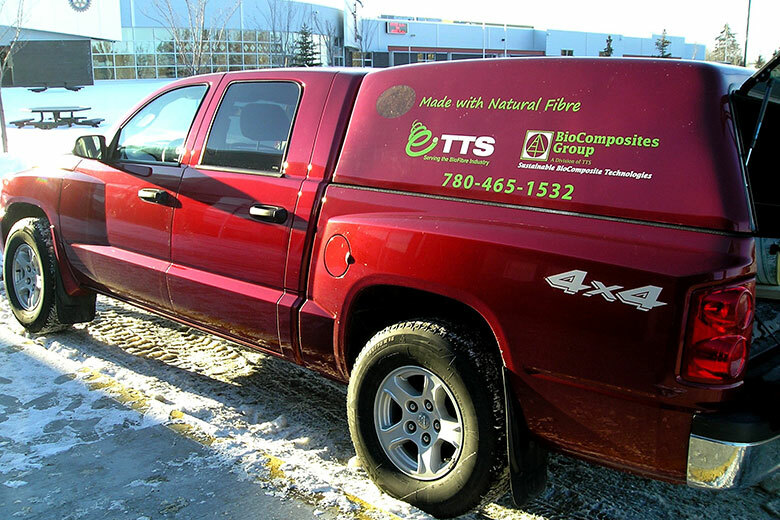
Figure vii – Truck canopy made of hemp fibre mats infused with plastic resins
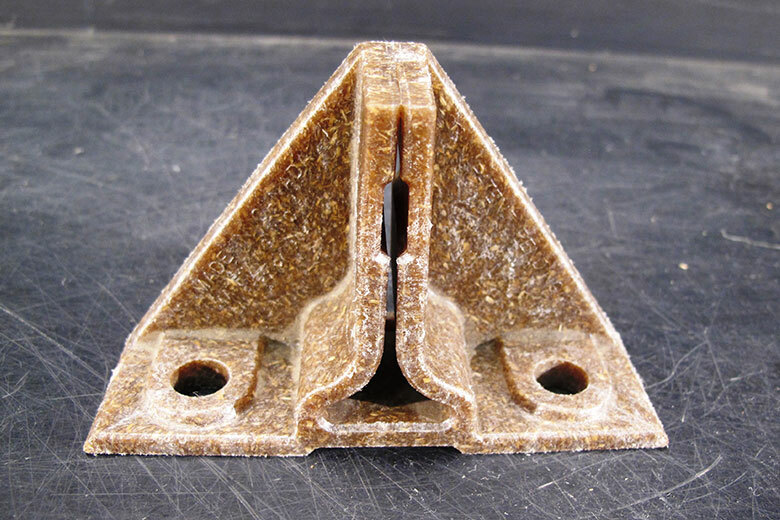
Figure viii – Example of injection moulded bast fiber composite part
- Textiles – The oldest application of bast fibre is re-gaining popularity due to its properties that cannot be matched by synthetic and several natural fibres (i.e. cotton). Please note that hemp for high quality textile applications often requires more demanding crop management and specialized decortication processing lines. Premium price should be achieved for appropriately prepared straw suitable for textile applications (Figure ix).
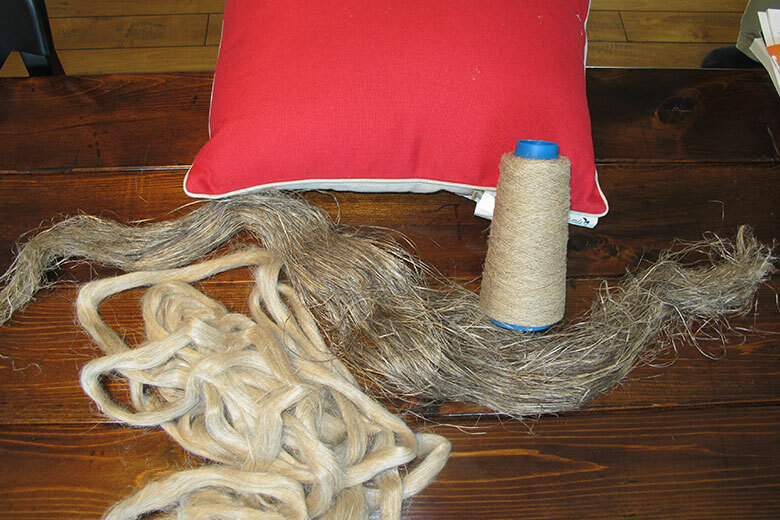
Figure ix – Hemp fibre, yarn and pillow case made of bast
- Insulation – Natural fibre materials provide good thermal protection. They are environmentally friendly and do not emit toxic, often allergenic chemicals found in synthetic insulation materials (Figure x).
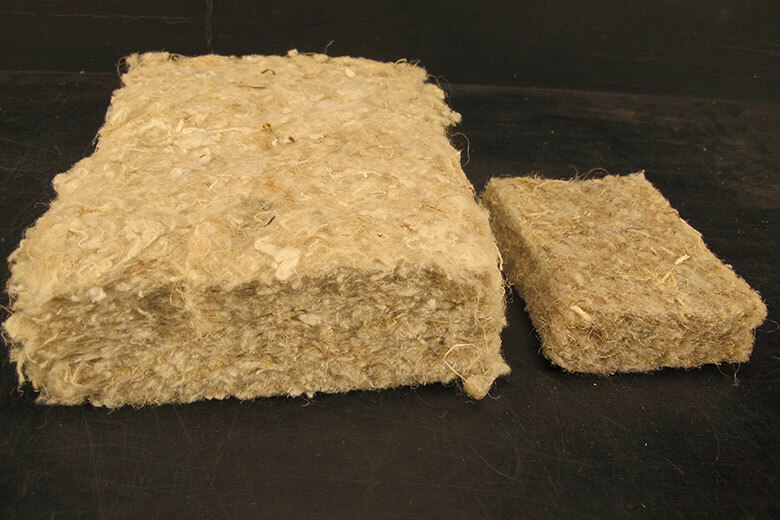
Figure x – Different grades of insulation materials made of bast fibre
- High grade paper – Revival of hemp cultivation will make available feedstocks for manufacturing of specialty, low volume, high value paper products.
- Twine, rope, upholstery – Lower grade, coarser bast fibre can be used for the production of tough fabrics and cordage.
Dust
Decortication of hemp stalks generates 10-15% of non-fibrous dust particles. After pelletization this by-product that has high heating value can be marketed as environmentally friendly fuel.